Saturday, 23 February 2013
Class On Kevin Rodel's Side Chair #7: Lower Stretchers

The Lower Stretchers
Note: When I talk about the many parts of this chair, I name them as if I were sitting in the chair.
Well ladies and gentlemen, I do believe we’re nearing the home stretch.
The lower stretchers consist of 4 parts. Two stretchers that run from “front-to-back” between the front and rear legs, and then two stretchers that run in opposite direction “side-to-side” between those first two lower stretchers.
Mr. Rodel’s chair plans call for a half-lap dovetail joint where the side-to-side lower stretchers meet the front-to-back lower stretchers.
Shortly after diving into the creation of the lower stretchers, I found myself stepping into the confessional once again.
I’ll be right upfront…I’m horrible at making half-lap dovetails. Especially “angled” half-lap dovetails. Let me go on record by saying that I tried…I really tried. But after many less than adequate attempts, I opted to go with just good ol’ half-lap joints.
That doesn’t say that I won’t learn how some day…I just didn’t have the time nor patience at this stage of the game.
Now that I’m out of the confessional and back into the shop, let’s dig in.
An important decision for me was to decide on how the grain would be viewed between these two different parts.
I liked the look of having the side grain on the front-to-back lower stretcher match that of the side grain of the front and rear legs. Then I decided that where the side-to-side lower stretcher meets the front-to-back lower stretcher, I wanted the grain to mismatch…showing off that joint just a bit more.
So in other words, the grain on the top of the front-to-back lower stretchers matches that of the front face of the rear legs and the back face of the front legs. Looking at the photo below, you’ll see that the side-to-side lower stretchers were rotated 90 degrees (in regards to their grain), forcing a nice grain mismatch at the half-lap joint.
Next it’s off to the table saw to rip plenty of long strips that will eventually turn into these stretchers. If you should decide to follow my grain suggestion above, make sure you take this into account while creating the two different lower stretchers strips on your table saw.
Once you have enough strips cut for the grain orientation for the front-to-back lower stretchers and the grain orientation for the side-to-side lower stretchers, it’s off to the chop saw.
Need I say that you should leave your lower stretchers plenty long? :)
Make sure you make plenty of spares. Seeing that I was making 9 more chairs, I whipped out at least a couple dozen of each type of lower stretchers.
The next step probably isn’t all that important, but I wanted to make sure that the nicest grain was facing “out” on the two front-to-back lower stretchers. A minor detail…but a simple task to complete at this stage.
(When someone eventually points at your lower stretchers and compliments you on the gorgeous grain, you can secretively say under your breath, “Yah…I know…I planned it that way.”)
Choosing the grain for the side-to-side lower stretchers wasn’t all that important to me seeing that you never know which side would be in view more…front or back. But you’ll always be looking at the outside surface of the front-to-back stretchers.
At this point I now have two piles of front-to-back stretchers (lefts and rights), and one huge pile of side-to-side lower stretchers.
As mentioned at the beginning of each of my chapters, all parts are marked as if I was sitting in the chair. So now it’s time to place an “L” and an “R” on the top side of all front-to-back lower stretchers. This assures me that they will eventually end up attached to my completed chair in the correct orientation.
Next I concentrated on the compound angle at the rear end of the front-to-back lower stretchers. As you’ll recall, the rear leg’s front surface goes down and back towards the floor at about a 2 degree angle. The front-to-back lower stretcher also runs between the rear and front leg at an 85.5 (or 4.5) degree angle, giving you your compound cut at the very rear end of the front-to-back lower stretcher.
It was so much easier for me to keep track of all the different cuts by actually marking the angles on the rear ends of each of the front-to-back lower stretchers.
(Don’t forget…the cuts will be “mirrored” for the left and right sides!!)
The photo below shows you how I marked the rear ends of the right side front-to-back stretchers with a “2” and a “4.5” for their respective angles.
This compound mitre cut can me made very easily at your table saw by using your mitre gauge and an angled table saw blade. My SawStop is a “left” tilting saw, so if you get oriented correctly as to how this cut is going to come out, I do believe this lower stretcher will end up being a “right” side lower stretcher. I agree…it’s a bit confusing.
The bottom line is…make one cut, check it to make sure it orients correctly with your chair, and then proceed with your mass production of either your left or right lower stretchers. Once done, you can then reset your equipment to make the opposite lower stretcher’s compound cuts.
Note: For those of you who are really paying close attention to the photo above, you’ll find one major mistake. This is a very poor example of a staged photo. I have the “outside grain” side of my lower stretcher facing in the wrong direction. It should be rotated 90 degrees with the nice grain facing my table saw blade…I think. :)
For those of you who noticed…you get a gold star for the day.
Before I move on to sharing more photos with you, I must mention one thing. I’ve discovered that it’s a bit difficult to create a woodworking class without showing photos slightly out of order at some point in time. So I have some explaining to do before you view the next photo.
When I took this next photo, I was quite a ways through my assembly stages. When it comes to creating the lower stretchers, you almost have to be at this same stage. Otherwise your parts just might not end up being their correct length.
So in the next photo, please keep in mind that the entire rear assembly (every part that falls behind your butt while sitting in the chair) is completely glued up. Plus the front assembly (the two front legs and the front rail) are also all glued together. And all parts in between are not glued up at all.
With all that said, you’ll notice in the photo below that I have now made a spacer that fits nicely between the rear and front leg. This 15 1/16 inch plywood spacer holds the legs exactly at where I want them to be while I cut my lower front-to-back stretchers to their proper length.
The compound mitre cuts are all done at this point, so all I need to do is sneak up on their final lengths by cutting another 4.5 degree cut at the front end of each stick.
Tip: You’ll know right away whether or not your spacer is correctly cut by looking for gaps in the joint where the upper side stretcher meets the rear and front leg. (Right where you see my web clamp in the photo below.)
And, once again, I must repeat those 3 famous words…consistency, consistency, consistency!! My rear legs were not all created equal, so my lower front-to-back stretchers all had to be made on a “per chair” basis. Aaarrgghh!!
Here is how I made each of my front-to-back stretchers:
1. I placed a light pencil mark on the outside surface of each rear and front leg marking the very center of my round mortise. (The mortise that will eventually take the dowel for each lower front-to-back stretcher.)
2. Then I placed another pencil mark on each front-to-back stretcher indicating where the center of the mortise would be on each stick.
3. Now I slowly snuck up on that final stretcher length by cutting just a little bit at a time at a 4.5 degree angle from the front end of each stretcher.
As you can see in the photo below, I have just a little more cutting to do before my mortises line up properly.
As the stretcher got shorter and shorter, I’d simply move the part up into place until the pencil marks all lined up. Once they lined up, I knew that the stretchers were at their perfect length and final home.
Remember back in the “Rear Legs” chapter I mentioned that I marked each pair of rear legs with a letter? Now’s the time that I also mark the front-to-back stretchers with that same letter.
For me, this was a very important step to make sure I had parts paired up right before glue up time.
One of the final steps for the front-to-back lower stretchers is the mortise. As mentioned earlier, I decided to drill a mortise in each end of the stretchers as opposed to a square mortise. Seeing that the mortise in the front and rear legs were drilled at the proper 4.5 degree angle, this means I can make a very simple “straight in” mortise on the stretchers.
A simple jig is all it takes to perform this task. In the photo below you’ll see that I have the stretcher tightly clamped in and parallel to my 5/8 inch Forstner bit. I went just a hair deeper than 1 inch allowing me to use a 2 inch oak dowel at glue up time.
Note: If you decide to make your side-to-side stretchers with the dovetail half-lab joint, then you can most likely skip the next section.
This step was rather fun for me. I really enjoyed making the half-lap joints not only because I knew I could, but also because I especially enjoy doing assembly line type work in my shop. A very gratifying stage in the chair making for me. Plus knowing that I’m nearly done with the creation of all parts is quite satisfying as well.
To assist in creating the two side-to-side stretchers, I made some spacers that allowed me to make pencil marks on both the top surface of the front-to-back stretchers, and on the bottom surface of each side-to-side stretcher. The pencil marks will assist in the making of the half-lap joints.
In the next two photos below you’ll see that I made two spacers for each side of the chair. The longer front spacer has the famous 4.5 degree cut on its front end. All other cuts on the spacers are 90s.
To keep things organized, I marked the front, longer spacers with an “R” and an “L”.
Note: In the photos below, the longer, front spacer is bumped up against the front legs.
With the chair dry clamped together, and your spacers and side-to-side stretchers in place, it’s time to make some pencil marks.
As mentioned above, the longer spacer is bumped up against the front legs. Next in line is the forward-most side-to-side stretcher, then the short spacer, finally followed by the rear side-to-side stretcher.
Important: Make sure your grain selection is oriented the correct way.
With the chair up on a work surface and while standing behind the chair, I pushed all 6 sticks tight up against the front legs.
With a nice, sharp pencil I now make marks on the undersides of both side-to-side stretchers. Eight marks in all.
Next I put downward pressure on the two side-to-side stretchers (making sure they don’t budge a bit) while removing all spacers. This gives me the room needed to mark the 8 pencil marks on the top surface of both front-to-back stretchers.
In the photos below I’ve flipped the side-to-side stretchers over to reveal all pencil marks.
The side-to-side stretchers can now be cut to length. I left my mine just a bit long as you’ll see in a photo later in this chapter.
Note that the two side-to-side stretchers will eventually be a little different in length from each other. The front one will be just a little longer than the back one.
To create the half-lap joints I return to my table saw and stacked dado blade set. Experiment with getting the exact width and height of your dado blades by testing it on a couple scrap pieces of stretchers. Once your side-to-side stretcher fits into your test piece, you know you’ll have a great looking joint.
Note: When I did a test fit on the half-lap joint on my test pieces, I left the side-to-side stretchers just a bit proud…or “high” in addition to being a bit long. This seemed to work out better for me as opposed to having them accidentally falling too low into the joint. Sanding them down to be perfectly flush with the front-to-back stretchers was a simple task.
You should be able to see what I mean by taking a look at the photo below.
As long as the chair is still clamped together, I decided to work on the half-lap part of the side-to-side stretchers first. I did this by setting my mitre gauge to 4.5 degrees, and then slowly whittling away the half-lap until I just barely snuck up on the pencil mark on the underside of the side-to-side stretcher. I did this identical end cut on the same ends all side-to-side stretchers.
Next I moved my mitre gauge to the opposite side of my dado blade, and then kicked the mitre gauge 4.5 degrees into the opposite direction to make the half-lap joint on the opposite end of all side-to-side stretchers.
While sneaking up on the pencil mark on the side-to-side stretchers, I would take the part over to the chair to make sure it fits snugly into place between the two front-to-back stretchers. Before you know it, you’ll have the half-laps completed on all of your side-to-side stretchers.
Once you’re sure your side-to-side stretchers fit nicely between the other stretchers, it’s time to remove your front-to-back stretchers from your chair, and take them to the table saw.
In the photo below you’ll see how I have my mitre gauge and dado blade set up for the half-lap cuts on the front-to-back stretchers.
I first set the mitre gauge up with a stop block that allowed me to cut the rear-most dado. If you stay between your pencil marks, you’re good to go. I would repeat this same cut on all right side front-to-back lower stretchers. Then I’d move my stop block to make the cut that is closer to the front leg of the chair. Again repeating that cut on all right side pieces.
A look from the other side of the table saw.
Here’s where I step back into the confessional. Let me set up this wood shop story with a bit of info. My SawStop is fairly new to me, The $190.00 Freud Stacked Dado Blade and $80.00 SawStop braking cartridge were both about 4 hours old. I had just taken delivery of both parts from Amazon. (Can you see where I’m headed?)
My next move in woodworking history will NEVER be forgotten. When I swung my “metal” mitre gauge 4.5 degrees into the opposite direction to make the second set of cuts, I did not realize that I had now placed the ever so tiny corner of the mitre gauge directly into the path of the dada blade set. And unfortunately, I did not have the computerized braking system turned off on my new SawStop table saw.
Long story short…in 1/5000th of a second, I had not only lost nearly $300.00 in brand new woodworking equipment, but I think I may have also created a few new words. Trust me, the braking system on this thing really works…along with an extremely loud BANG!!
Now, where did I put those clean trousers? :)
Here’s a photo of my “reminder trophy” that hangs directly above my saw.
Off to the tool store for a new dada blade set and 8 inch SawStop braking cartridge. :(
Jumping ahead to assembly time, you’ll see in the photos below how my side-to-side stretchers were left a little long, and what they looked like after a very short meeting with my orbital sander.
(The chair is laying on its side in both photos.)
See you at the next chapter…
Dale “Gramps” Peterson.
Crafty Puzzles
Hungry Eye Optical Illusion
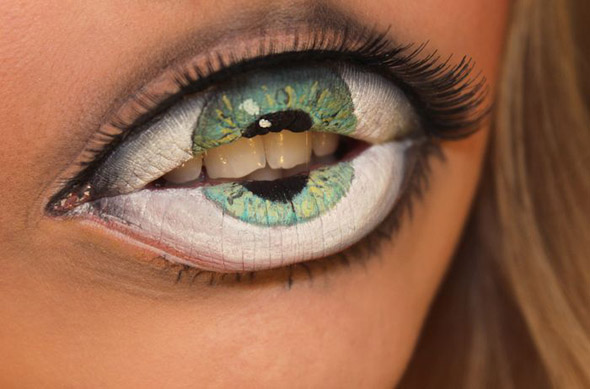
An excellent photograph was sent to me by Marcus yesterday. After a while the magic disappeared – since longer I observed it, less illusionary it felt. Still, I remember firmly how strong and puzzling was the moment I first glazed my eyes over the photo. For a second there, I trully couldn’t understand what was going on. Hope your first “stare” brings as much surprise and joy as I experienced. Don’t forget to share your first impression in our comments below!
Crafty Puzzles