Thursday, 28 February 2013
Game Calls #2: Scratch Box Turkey Calls

After posting a few of these neat little calls I thought some other folks might like to know how to make them. They are an easy project and another way to use some of that scrap wood.
The easiest way to make a scratch box is to have a dedicated mortiser set up with a 1/2”cutter but since I don’t have one here is how I do it. If you do have one you can quickly see how to use it to accomplish what I am doing.
I start with a 1 & 5/8”“x4” piece 1/2” thick. I cut out the center on my bandsaw leaving about 3/8” or less for my frame. I cut 1/8” to 3/16” thick pieces for the sides, one side is the same height as the frame and the other is 2” high. The wider piece will be your sound board.
Glue the short side on then smooth the top on your sander, next glue the sound board on. You also need to cut a thin piece to cover the opening on top of the call then sand or cut a slot on the side touching the sound board to let the turkey out. Pay no attention to the GOOP sitting on the table that is for something else. I use Tightbond III to glue these up.
Once everything is glued up all you need to do is go back to the sander for shaping and tuning. The shape is up to you but the tuning is done the same way each time. You thin the sound board to 1/8” or less then using a piece of wood 3/8”x3”x about 1”wide that has been chalked you hold the call upside down and pull the sound board toward you. If the call is too high pitched take a tiny bit more wood off and test again. Do this until the turkey comes out. Go slowly here it is easy to ruin your call at this point.
This is my test stick which is a scrap of cherry I roughly domed and chalked. I use it in the shop since it is easier to hold while testing a lot of calls. When testing the sound board should be on the side away from you as you pull it toward you.
After you have it tuned do a bit of finish sanding and apply whatever finish you like. If you have any questions feel free to ask. Thanks for reading.
Crafty Puzzles
Manfred Stader’s Cup of Coffee
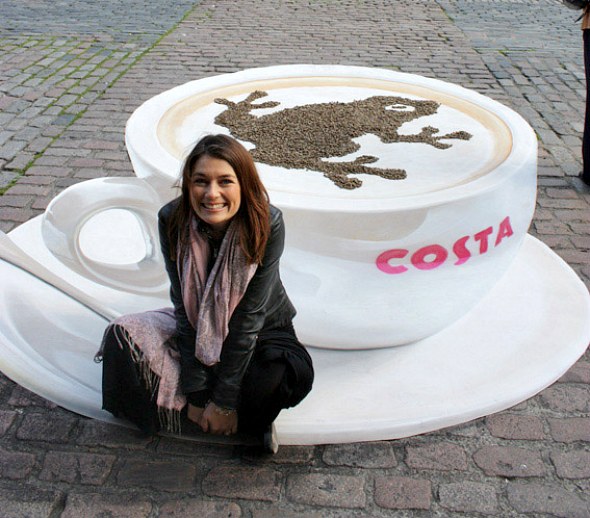
For those of you who never heard of #Manfred Stader, he is one hell of a talented chalk artist. If I remember well, he even turned his talent into a full-time profession – travelling around the world, painting streets with unique chalk drawings that appear 3D if you look at them from certain perspective. Here’s a cup of coffee he did for Costa:
Crafty Puzzles
Answer - Week 9 - Monday - British Mensa
via Crafty Puzzles http://www.mensa.org.uk/cgi-bin/item.cgi?id=2656
Mensa Brainteaser - Week 9 - Thursday - British Mensa
via Crafty Puzzles http://www.mensa.org.uk/cgi-bin/item.cgi?id=2655
Wednesday, 27 February 2013
Speedy glue up of smaller parts.
I’ve been wanting to share this little tip for quite some time. My father showed it to me about 20 years ago or so and I have yet to find another woodworker who has heard of it. I do a lot of small projects in my shop, from fretwork to puzzles and beyond. I’m always needing to glue some little parts together and don’t have the patience to wait for em to dry. That’s where this trick comes in. The microwave. When gluing up your work get the pieces positioned to where you want them. This works if the parts will fit in a microwave of course. Put a piece of wax paper in the microwave and carefully set you glued up pieces in making sure they are still positioned properly. Nuke em for no more than 15 seconds. Take theme out and make sure they’re still positioned correctly and clamp if needed. This can cut your wait time down to a easy 30 minutes.
My interpretation of what happens is that the microwave causes the wood to expand a bit due to the moisture in it thus pulling the glue into the wood for a deeper, quicker bond. I’m no scientist so my theory could be wrong, but …it works.
Crafty Puzzles
Tuesday, 26 February 2013
Game Calls #1: Turkey Friction Call

Well, thanks to the comments and questions I have gotten I dug through my pics to find one I had on how to make a pot call. So for the folks that want a quick tutorial here we go.
A pot call is basically a shallow dish containing two ledges inside. One is cut into the rim to hold the playing surface while the second is a ring left in the center raised to clear the bottom of the pot and still leave a space between the sound board that rests on it and the playing surface above it.
One thing not shown is how tall the call is, that would be 3/4”. Another is the rim at the bottom is 1/8” high.
These dimensions are fairly critical in how a call sounds. You are building a musical instrument so minor changes will make a difference. One question all new makers ask is if different woods give different sounds and the answer is, yes. The density and hardness of the material you use does change the vibrations you create. Another big one is sound board or no sound board. Again what you use makes sound changes. You can use almost any material you use as the playing surface for a sound board plus wood, acrylic and plastic. The sound board is smaller than the playing surface to leave a small gap between the inside walls of the call and the sound board. You can choose to leave the sound board out, too. An example is what I use, playing surface is 3 1/2” while the sound board is 3”.
The holes in the bottom of the call can vary widely, from a single hole to 8+. You can place them in patterns you like and vary the sizes. The number and size will change the sounds.
The playing surface and sound boards need to be glued into place. Almost all call makers use GOOP to do this. It is far better than other glues so I would suggest sticking with it. Get it sticking with it, it’s glue and it sticks stuff. ;-)
You can turn these using a face plate with a screw but the easiest way is with a chuck which I finally bought a few weeks ago. I drill a 3/4” hole in the center using a Forstner’s bit the mount it on the lathe. After getting things round I trim the piece to 3/4” thickness then start hogging out the wood in the center.
This is a show call that is why it has wings. Not a useable piece I was just messing around but you can see how it sits on the lathe.
I make the rim at the edge first then clean out the whole call to the depth I need leaving the ring in the center. After that I flip the call and do any detailing I want on the outside and sand to finish. There is nothing really hard about these and after one or two you can turn them fairly fast. In fact you can do this process reversed, doing the outside of the call then flipping it to do the inside.
Once I have this it is back to the drill press for sound holes if needed then to the finish table. Most of mine just get rattle can lacquer or WOP. I do use a natural stain before applying the clear.
You can also turn your striker to play the call. The woods used for these change everything again. Do not sand the tip too much as the small scratches cause the friction you need. You will also need to scuff the playing surface with a 3M green pad.
Strikers vary widely and I will do another post on them later.
Crafty Puzzles
Monday, 25 February 2013
Mensa Puzzle Tweet Answer for 25/02/13 - British Mensa
via Crafty Puzzles http://www.mensa.org.uk/cgi-bin/item.cgi?id=2642
Answer - Week 8 - Thursday - British Mensa
via Crafty Puzzles http://www.mensa.org.uk/cgi-bin/item.cgi?id=2653
Mensa Brainteaser - Week 9 - Monday - British Mensa
via Crafty Puzzles http://www.mensa.org.uk/cgi-bin/item.cgi?id=2652
Sunday, 24 February 2013
Folding Scrabble Turntable

Several years ago, I started designing a somewhat elaborate Scrabble storage box that was also going to serve as a game turntable. The top of the box was split into two fold-out wings that would support the board during game play, the bottom would provide storage the the original paper box, and the whole thing would rotate.
I never finished designing, much less building, that box, but I did build this very simple folding Scrabble turntable out of some scrap wood, a 3” Lazy Susan bearing, two 3/4” brass hinges, and some rubber furniture bumpers. As you can see, I focused exclusively on function, and didn’t worry much about appearance. I didn’t even apply a finish.
Both the base and the support panels have a shallow (about 1/16”) recess for the bearing. The bearing is glued to the base. To play, we just place the base on the kitchen table, place one of the support panels over the bearing (it’s easier to line things up this way), then unfold the other panel. The turntable spins easily, but not so easily that the tiles fly off.
It has served us well. It keeps the playing surface pretty close to the game table, and it stores easily. The turntable base fits into the game box, and the folded top is roughly the same size as the box.
I haven’t seen anything like this out there, so I thought I’d describe it here. I can see prettier versions of this design being good gifts for the Scrabble fans in your life.
Crafty Puzzles